Antipyretics for children are prescribed by a pediatrician. But there are situations of emergency care for fever, when the child needs to give the medicine immediately. Then the parents take responsibility and apply antipyretic drugs. What is allowed to give to infants? How can you bring down the temperature in older children? Which medications are the safest?
The dominant position in the furniture market is occupied by facades of MDF, processed by a film method. Their relevance is associated with a huge variety of designs, limitless design possibilities and moderate cost, which is sometimes the decisive factor. The reason for the main advantages of the popular type lies in the manufacturing method and technical characteristics that are optimally suited for the production of kitchen furniture.
There are many types of furniture, with which you can comfortably surround the room for cooking or eating. The first place is occupied by budgetary and comfortable sets of wood fiber boards, strong enough and wear-resistant to last more than 10 years.
Beautiful modern interior in budget execution
Advantages of laminated and veneered materials were quickly appreciated by designers, and hundreds of new furniture configurations, ceiling casing, interior doors, window sills, facing details appeared on the market - they are all perfectly suited for furnishing and complex finishing of the premises.
Worktop-sill: space saving
Advantages of MDF facades in PVC laminating film:
- high degree of strength - 2-3 times higher than the parameters of chipboard and slightly lower than the characteristics of natural wood;
- wear resistance - no deformation and preservation of the properties of the decorative layer, despite the high humidity and constant temperature fluctuations;
- moisture resistance - a consequence of sufficient density and additional impregnation by special means;
- possibility of milling, patination and other methods of decorative processing;
- simplicity of assembly and installation by one's own hands;
- availability - low cost compared to products made of solid or plastic.
The disadvantages include the use of special fasteners, weak load-bearing capacity, high weight (in comparison with wood), the presence of formaldehyde in the adhesive composition.
Production technology of MDF panels
Since the American engineer UG Mason created the first prototype of a wood fiber board, it took almost a century. The way of manufacturing MDF has changed several times, and today we see the end result - a solid and reliable basis for the production of furniture. Let's consider all stages of production.
Manufacture of wood fiber
The production of wood fiber is a complex technological process that requires the processing of wood on special equipment. First, the trunks of different breeds are cleaned - remove the bark, branches and branches in the drum machines, then the logs are cut into chips of a certain fraction in the disintegration chambers. Any chips are not good, so it is sorted: the small is harvested in a bunker for burning, the large one is cut again.
One of the shops of the plant for the production of MDF
Elements of a suitable size are thoroughly washed, freed from mineral impurities and debris in a vertical installation, then treated with steam and saturated with moisture at a temperature of +100 ° C. It is necessary that the moisture content of the raw material reaches 80%.
Further in the process is included defibrator - auger plant with a large number of blades of various shapes. Blades for several cycles share the hot and moisture-saturated chips on individual fibers. In order for the fibrous mass to acquire the necessary characteristics, at this stage paraffin, resin, hardeners and binders are added to it.
The next stage is a dryer in which hot dry air removes excess moisture from the mass, reducing the humidity to 9%. At the last stage, the fibers get rid of air, making the mass denser. After that, it is ready to be formed into standard blanks.
Forming and pressing plates
Pressing is a long stage, consisting of several parts. First, the mass, which moves along the conveyor in the form of a shapeless carpet, is pressed in the usual way by means of several rows of rollers - so remove the air remains.
Pressed plate without decorative processing
Then, more powerful, hot pressing is carried out, which forms the technical characteristics of the plate:
- stiffness - the mass is compressed by a metal plate at a temperature of 210-230 ° C under a pressure of not less than 350 MPa;
- strength - under a pressure reduced by 3 times and temperature slightly below 210 ° C;
- calibration - the thickness of the layer, at low pressure and without additional heating.
As a result, a sturdy, dense, ready-to-process plate is obtained, which remains to be divided into sections convenient for transportation and storage. Cutting is done with large circular saws, after which the workpieces are laid on wide racks. For half an hour they completely cool down.
Samples of blanks after lamination
After passing several stages of a powerful but not enough delicate press, the MDF panels require additional alignment. To make the surface of the products perfectly smooth, without changes in thickness and irregularities, they are ground on surface grinding equipment. The finished plates are labeled and sent to lamination. Some of the products are immediately sent to the warehouse, since it is already ready for use (wall panels).
Lamination as a way of processing
All products, from which film facades are subsequently produced, require additional processing, otherwise without surface protection under the influence of high temperature and humidity, the fibers will again change their structure and deform. The process of pasting with a decorative polyvinyl chloride film is called lamination. A firmly adhered polymer increases the resistance to mechanical attack and protects the adhesive layer from sunlight.
Modern built-in furniture from MDF
The second way of processing - veneering, finishing with thin sheets of natural wood. The cost of veneered products is slightly higher. As the glue used all the same phenol-formaldehyde resins, so neither film nor veneered products can not be called environmentally impeccable.
Glossy glare is very similar to a more expensive plastic
The main advantage of both types of furniture boards is the ability to imitate natural wood and receive many other interesting decorative solutions, while the cost is much lower than that of the array.
PVC films for furniture facades
Without a PVC layer, which fits tightly the details of kitchen sets, the furniture would not be so attractive and functional. In order to better navigate the range of film coatings, we will consider their technical characteristics, types and technology of application.
Types and characteristics
Standard dimensions of a roll of vinyl chloride film for furniture production:
- width - 1.4 m;
- length - 100-500 m;
- thickness - 0,15-0,80 mm.
The main qualities - strength, elasticity, low level of thermal conductivity, moisture resistance. Some types have rigidity, in which furniture is not threatened by mechanical damage, no abrasion, or rapid wear. If the lamination process is carried out without disturbances, the PVC film on the facades for the kitchen will last for 10-15 years, and when peeling it can be glued back without changing the decorative properties.
Imitation wood for choice
Chemically treated polymer becomes an additional protection against wood and food bugs, mold and fungus.
Laminated Kitchen in Classic Style
According to the technology of applying PVC film is divided into the following categories:
- for laminating smooth surfaces without images and relief (thickness not more than 0.3 mm);
- for membrane-vacuum pressing when creating an invoice surface or imitating natural materials (thickness no more than 0.5 mm);
- for lamination - one- and two-layer coatings (thickness 0,3-0,5 mm);
- for facing the edge and end surfaces.
According to the degree of light reflection, there are matte, glossy and highly glossy surfaces; by type of embossing - smooth, with a slight embossing, with a deep texture. The palette of MDF samples is unlimited: from white and black to the most vivid shades. Manufacturers provide a choice between monochrome and mirror products, imitation wood or stone.
Respectable Italian and German companies for the production of PVC finishing materials compete with Chinese and Korean enterprises, offering lower prices and acceptable quality. Also, you can often find cladding of Japanese and Taiwanese origin.
Methods of application
Depending on the type of coating and the type of subsequent decoration, one of the following finishing methods is selected:
- laminating - gluing under the vacuum press, the cheapest kind of lining;
- lamination - the process of gluing the decorative layer under the influence of strong pressure and high temperature, more reliable than laminating;
- postformirovanie - full-fledged finish panels flat film without images, the characteristics are ideal for the manufacture of countertops.
Terms are of a highly specialized nature, in everyday life all three types are called lamination.
Worktop with post-formed lining
When choosing a headset, you can ask how the product is manufactured, since laminated or postformed products serve longer than laminated counterparts.
Decorative design of facades MDF
In addition to a very moderate cost, MDF sets are attracted by a variety of decorative finishes, which impart exclusive and stylish style to furniture. A variety of textures, unusual relief, photo printing, a rare shade, a strong varnish coating - if desired, your budget option will look no worse than an expensive construction of plastic or natural wood.
Manufacturing of bent elements
Design projects or planning features often require configurations with rounded parts. Unlike rigid plastic, MDF elastic panels with a thickness of 0.8 cm can be smoothly bent, connected together and get bent parts. One of the techniques is the gluing of two notched sheets on the back, which serve as the basis for the production of blanks with a thickness of 1.6 cm.
Ready dried and cooled billets
For the production of smooth, bent for a given radius of workpieces use special format-cutting equipment, equipped with ready-made templates. The process of bonding individual sheets occurs under vacuum pressure for an hour at a temperature of up to 60 ° C. Sometimes instead of two take a few thinner sheets, but the strength of the product does not suffer from this.
Tightening of PVC with foil or milling occurs after cooling of the bent parts.
Technology of facade milling
Milling - is the treatment of wood or wood fiber boards with a cutting tool to improve the appearance or functional qualities.
The milling is made with a CNC machine
Milling is carried out in three stages, processing various parts of the blanks:
- angles - to remove sharp protrusions and prevent injury;
- edge - to give a certain form and further facing;
- surface - for the purpose of drawing a picture.
The exact artistic drawing can be obtained only when using a CNC milling and engraving machine. The program is introduced with parameters that provide the motion vector of the cutters, which quickly and accurately cut out the given image.
Linear milling is typical for classic sets
After milling, the finishing is carried out - grinding, with the help of which remove excess villi and scratches.
Frame "MDF frame"
To decorate cabinets with glass, decorative panels of a different shade or mirrors, a special design is needed - the MDF frame. This is an inexpensive addition, which is often used for dyed and laminated products. The framework, like the rest of the surface, can be milled, patinated, applied images.
Manufacturing technology:
- cutting of blanks from the plate;
- cutting ends at an angle of 45 degrees;
- cutting out grooves for fastening and inserting glass;
- decorative treatment.
The width of the groove for securing the glass or panel is about 8 mm.
Inexpensive corner kitchen in contrast frame
Making frames is a simple procedure that you can do yourself, so this element is often decorated with self-designed kitchens.
Patination - aging effect
If you want to order a truly exclusive and exquisite project, pay attention to patinated products. The effect of the aged tree is perfect for classical interiors and country furnishings, suitable for baroque, ampi and loft.
Patinated on a fibreous basis
The processing technology is complex and time-consuming, so the implementation of the project is more expensive. Not all entrepreneurs take up work that requires a certain degree of certain skills, but if you are lucky with the performer, the result will be excellent.
Some master craftsmen manage to perform patination independently, which does not differ from the factory one (which, by the way, is often also performed manually). The technology is simple:
- application of adhesive primer;
- treatment with polyurethane impregnation for patina;
- grinding;
- application of patina (special paintwork);
- treatment of patinated surfaces (sponge, brush, nazhdachkoy);
- varnishing.
Patination is often combined with milling, processing the decorative composition of the hollows or projecting details.
The secret of facades in 3D format
Applied to furniture sets 3D format is a visual three-dimensional design of facades. It can be achieved in various ways, but for MDF there are only two:
- milling with deep knives;
- the application of a volumetric image with paints followed by lamination.
In the free sale of such products are rare, they are often ordered by one of the samples. On the plane is cut not just a drawing, but an effective three-dimensional image, interesting for visual perception.
3D effect made by milling
There is a special kind of panels with the same type of repeating pattern, processed by milling along the entire width. The three-dimensional ornament carries the names of elements, which it reminds: "bark", "wave", "dunes", "flame", "braid".
Design of wall cabinets in 3D format
A separate group consists of surfaces, decorated with the method of photo printing. The image is applied to a specially primed layer, then covered with a varnish or a laminating film.
Maintenance of laminated panels
Often the cause of loss of decorative properties of film products is improper care. MDF panels, like any multi-layer structures, are afraid of aggressive cleaning agents. Liquids, emulsions and gels with solvents quickly cause the film to become unusable, and abrasive particles of powders cover the beautiful gloss with scratches.
Plaque can be removed with a damp cloth
- keep a comfortable temperature regime (do not heat above + 60-70º C, do not leave for a long time at minus temperature);
- exclude powder detergents, as well as formulations with solvents and bleaches;
- establish ventilation to establish a normal level of humidity;
- clean with mild soapy solutions, then rinse and wipe dry.
The microclimate in the kitchen or in the dining room, according to the parameters suitable for a comfortable stay of a person, is also good for film constructions.
Possibility of repair or restoration
One of the most common problems is film peeling. Adhesive layer is destroyed for various reasons: due to frequently used aggressive detergents, sudden temperature fluctuations, high humidity of the air in the room, proximity to open fire.
A common defect is flaking of the edge
If a small area of the front panel or a piece of edge is peeled off, you can make a restoration yourself:
- purchase "liquid nails", "super-torque" or glue PVA;
- draw a bit of adhesive in a medical syringe;
- carefully insert the solution under the film (or apply to the edge);
- iron and press the top layer.
Sometimes the film coating not only lags behind the base, but also deforms - shrinks or folds. In this case, the help of furniture makers will be required, since it is quite difficult to replace the door completely or the countertop on an identical one.
If the repair area is large, take advantage of the situation and completely change the lining - as a result you will get a new kitchen, different in shade or texture.
Design of kitchen interiors with MDF facades
A variety of finishing methods and outstanding technical characteristics allow creating numerous projects, differing in design, interior filling, and exterior decoration.
With the help of film technology, it is easy to assemble a kitchen in a classical style: gentle shades, easy milling, imitation of wood texture.
Postforming and gloss are more suitable for modern technical styles: smooth reflective surface, straight geometry, metallic shades.
Bright high-tech
Facades with milling in a modern interior
Narrowly rubbed planes, aged carved images, a pastel palette or a "wood" decor - and before you a warm and cozy country style.
A rustic design
A bit of "marble" or "granite" (popular in the finish of countertops), natural colors, simple modern design - ready loft.
If you want romance - order photo printing on the front or the panel for facing the "apron".
Finally a bit of interesting information about kitchen facades in general and film MDF in particular:
Useful thematic information:
Professional patination:
Example of a budget kitchen with film facades MDF:
As you can see, solid MDF boards in film "packaging" are a great chance to design the kitchen of your dreams. Decide on the style, think over the design of the kitchen according to the layout, pick up the texture and color and boldly order a set of built-in furniture! If you have any questions, please contact the designers who will help you compose the project and calculate the cost of the headset.
Furniture facades with decorative milling
Milling is a popular mechanical method for processing furniture facades. With its help, surprisingly aesthetic elements for modern kitchen sets are obtained, which means that even democratic furniture gets a chance to be attractive and stylish.
Algorithm for creating a milled facade
At the first stage of the sheet material directly created kitchen facades - the material is cut to the size of the customer. Then the workpiece is sent for machining. A special milling machine applies unique furniture patterns to the facades. Depending on the project, it can be all kinds of drawings, straight or curved lines of different depth, thickness and profile.
If you milled the facade MDF, then after applying a relief pattern, the surface is covered with a special film and laminated. This allows you to achieve amazing aesthetic characteristics. Milling facades for a kitchen economy class will make the budget set a worthy competitor of solid expensive furniture. At least, their external data will be similar in many respects.
Equally luxurious are the cabinets with milled facades. If you are not a fan of mirror doors, milling will make furniture design more interesting.
Types of milling facades
Milling of furniture facades is a great way to emphasize a single stylistic accessory, to emphasize rhythmic repetition of decor elements. If there are stylish relief designs on each cabinet at the top of the kitchen set, repeating the images on each drawer at the bottom of the headset - this furniture looks very attractive and harmonious. The most popular variants of milling facades of MDF are:
- Waves,
- Arches and semi-arches,
- Rectangular and rounded frames,
- Rectangles and rhombuses with bars,
- Ovals and strips.
Choose the picture that you like most, you can by photo in the catalogs of companies, or by personally studying the samples of milled facades, presented by furniture manufacturers.
Argument for acquisition kitchens to order with milled facades is its price per square meter. It is absolutely adequate, and thanks to the flow production is not much different from the cost of kitchens with smooth facade surfaces.
Modern materials make it possible to produce beautiful furniture. MDF facades are a plate, manufactured by pressing small-dispersed wood shavings with the addition of organic binders that do not contain harmful resins. They are used in the production of furniture and for finishing the premises in the form.
Furniture facades from MDF
Modern fine-grained slabs are suitable for the production of the finest furnishings:
- kitchen doors;
- office furniture;
- facades of hallways and living rooms;
- facial parts of sleeping cupboards;
- wall panels.
On the finished sheet is applied a protective layer of PVC film or varnish, which ensures that the product will last a long time. Many shades can create different color solutions, the door can be processed on a milling machine to create on the surface an invoice pattern, facets, rounded faces. Facades of MDF with gloss have an attractive reflective ability, are a fashionable aesthetic version of products in modern design. Doors play an important role in the design of the interior of any room.
When arranging the dining area, special attention is paid. Kitchen facades from MDF perform a practical and decorative function, are part of the architectural solution. They are of low cost combined with strength and durability. Such products are resistant to moisture and temperature changes, which is important for the kitchen, they do not burn out in the sun.
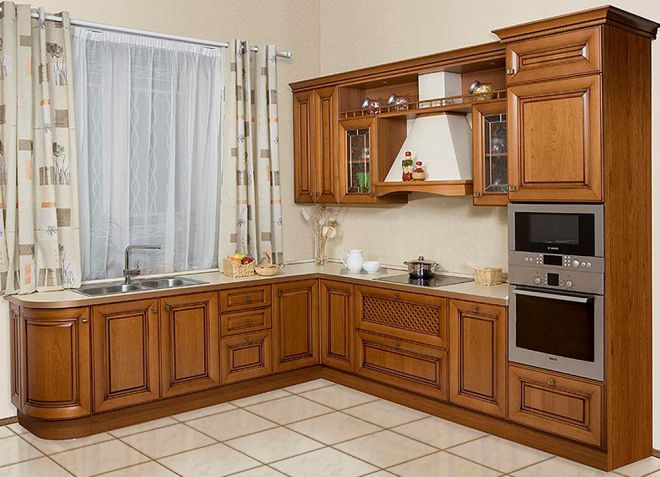
From the plate, doors of different shapes are produced - curved, wavy. Of these, it is easy to create hinged and floor pedestals with rounded edges. For finishing apply different types of varnish: from matte to glossy and mirror. The more layers of coating are carried out, the stronger the finish. For classical cuisine, the material is veneered under a tree. In this case, the door can be painted or preserved the texture of natural wood.
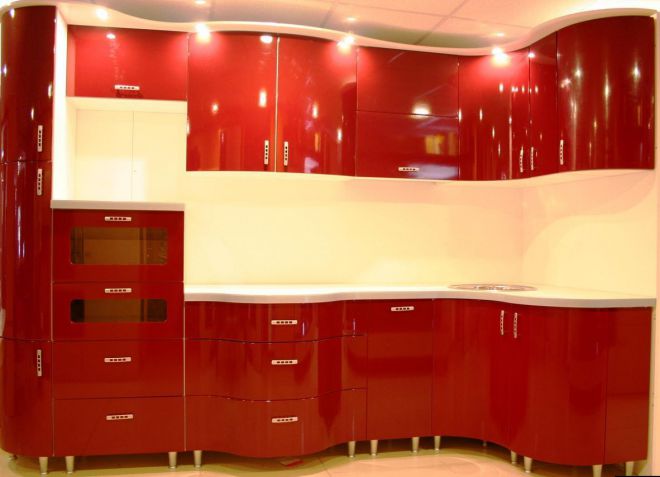
The design of furniture doors largely depends on the material of their manufacture. Furniture facades for MDF coupe are deaf (matt, glossy) or combined with glass or mirror inserts. Popular application of leather, rattan or bamboo elements on the slabs of facades MDF. According to the design options for the combination of parts are rectangular (vertical or horizontal), diagonally, along a straight line, wave. Mirror or glass inserts are often decorated with sandblasting patterns, toning. Panels can be decorated with photo printing.
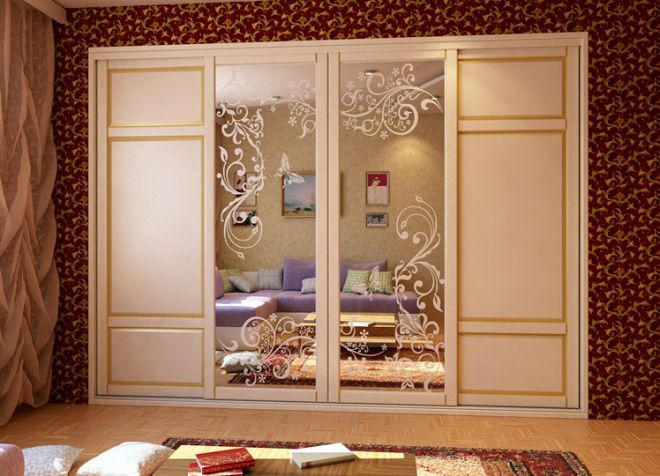
Products from pressed wood shavings combine functionality and beauty. The doors for the chest more often have classic MDF facades, decorated with milling, overlays, brass or old fittings. The color of the products includes all shades of natural inexpensive or exotic wood, veneers are used for their production.
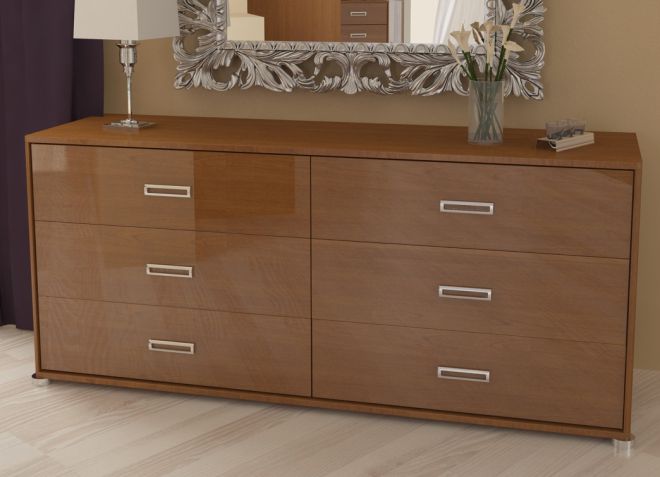
Types of MDF facades
Modern products from pressed wood boards have their advantages:
- durability;
- relatively low cost;
- resistance to moisture and fungi;
- ease of maintenance;
- wide design possibilities.
There are many technologies for processing plates to give them a beautiful appearance. The doors are decorated with a film of different colors, painted, glued with glossy plastics. covered with a natural layer of wood with subsequent varnishing, they are a complete replacement of wooden furniture. Classical products are milled to get a relief pattern, there are frame structures that are filled with different inserts.
Painted facades of MDF
The construction market offers a wide range of materials for beautiful furniture finishing. are obtained by coating the base with enamel or lacquer, their main feature is a perfectly smooth and smooth surface with a rich color. Color palette - the widest, you can choose a shade that fits the interior. They are monochrome or with an artistic drawing in the form of flowers, twigs, imitate a tree such surfaces can not.
The coating becomes matte or in the form of gloss, can have the effect of "mother of pearl", "pearl", "chameleon" or "metallic." Glossy MDF facades are covered with colored plastic, designed for those who love exclusive design. This is one of the most successful solutions for furniture in the Art Nouveau style or minimalism. Painted surfaces are resistant to burnup when exposed to ultraviolet rays. Plates with photoprinting, which is applied to the door and protected from above by a layer of varnish - an interesting way to make the interior unique.
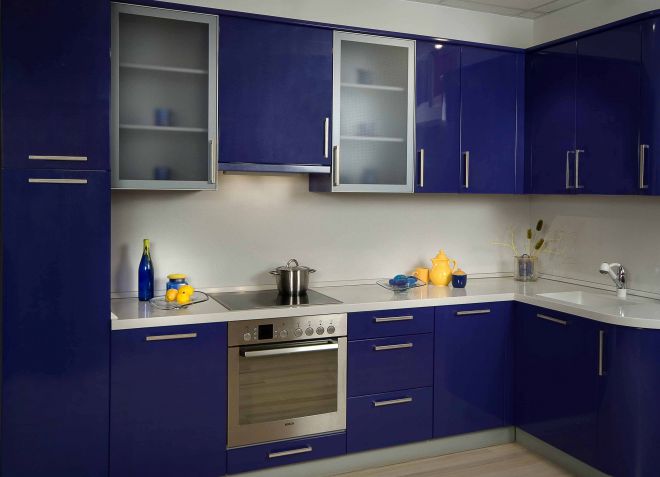
Products have gained popularity due to their low cost and wide palette of colors. Film plates are considered the cheapest in their segment. They are monophonic, with wood decor, have a matte or glossy surface, the effect is "metallic." often decorated with a structure for wood, marble, leather, textiles. They can be milled and give the headset a classic look. And applying a patinated varnish will help create an effect of antiquity. Film material is gentle - does not like high and low temperatures.
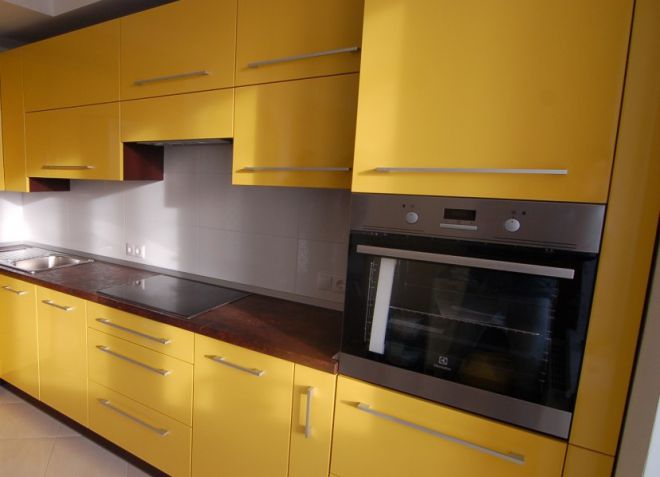
There are doors that consist of several constituent elements. from MDF are created with the help of the profile, from which the edging of the product is made, and various inserts. These are prefabricated doors, for their manufacture a thick plate and modern technology are used, over time the doors of the headset do not crumble and do not deform.
A frame made of MDF is placed in the frame, it can be decorated with a milled pattern, it is possible to combine colors if the interior is made of a different tone. Edging facades MDV can be made in a wide or narrow version, with sharp or smoothed corners. Instead of a plate it is possible to insert elements from a glass in a door, wooden lattices, a rattan are popular.
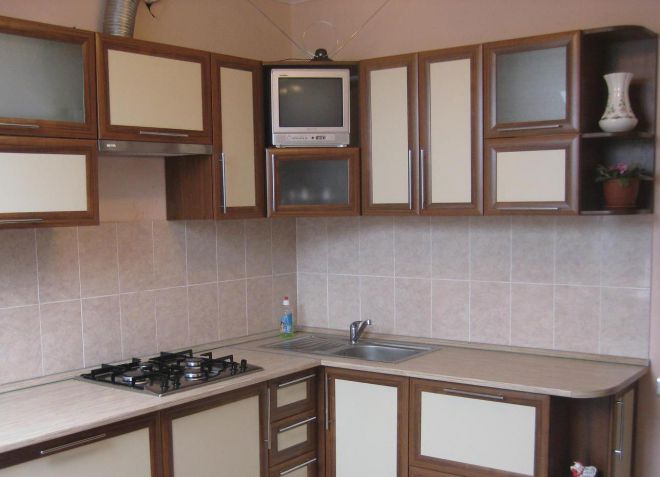
The advantage of the plate material is that it can be deformed on a special press. Curved facades made of MDF give the furniture design originality. They are made in the right color, with any radius of bending, they are film or painted. On curvilinear products, it is possible to create paneled drawings or to make it in bright form with a glossy coating. There are external and internal bends, with the help of which furniture corner structures of any configuration are created. They find application in the luxurious Baroque style, in modern high tech and modern.
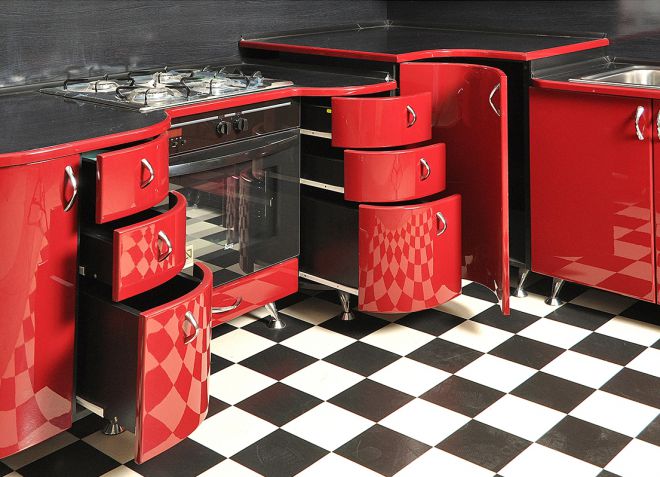
The surface of the door can be subjected to additional finishing: aging and subsequent varnishing. Patination of MDF facades is made using a special material with the effect of silver, bronze or gold and applying a fixing layer. Patterns and panels on these doors look more significant and acquire a touch of antiquity.
More expensive technology allows to achieve the effect of patination and the formation of cracks. For greater stylization, antique elements are used in the form of curly overlays with monogram drawings. Effectively it looks white furniture with a patina effect in the style of a provence or retro, a set with glass inserts, golden accessories.
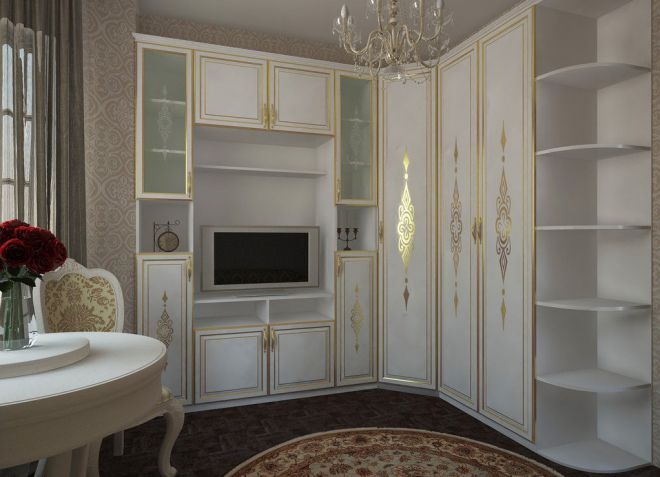
Modern fashion dictates the need for the emergence of new technologies. 3d plates have a three-dimensional relief, which simulates:
- tree;
- skin;
- sand dunes;
- wave;
- rhombuses and trapezium;
- flames;
- rock;
- various symmetrical drawings.
Patterns are made using 3D milling. Plastic facades MDF covered with a film (wood, glossy, matte, metallic), can be painted in any color. The products are complemented by laconic handles, if desired, the doors use the tip-on system, they can be opened only when touched. Such headsets are appropriate for modern design.
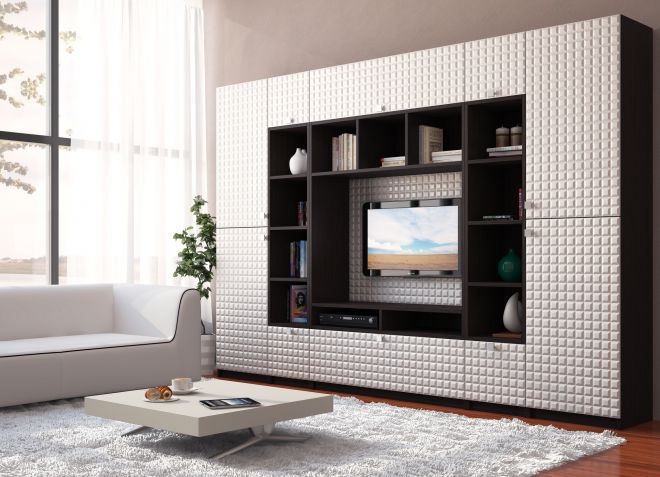
Any doors can be combined with inserts and overlays. Furniture facades from MDF decorated with glass - patterned, transparent, matte, colored or decorated with sandblasting patterns. It is used in the form of a panel, inserted into the frame of veneered material. The doors can be made in monochrome color, the use of photo sketches is allowed. Such products are glossy, ideal for modern design. Glass in the form of lattices with a gilded texture, inserted in a frame, will decorate any classical interior.
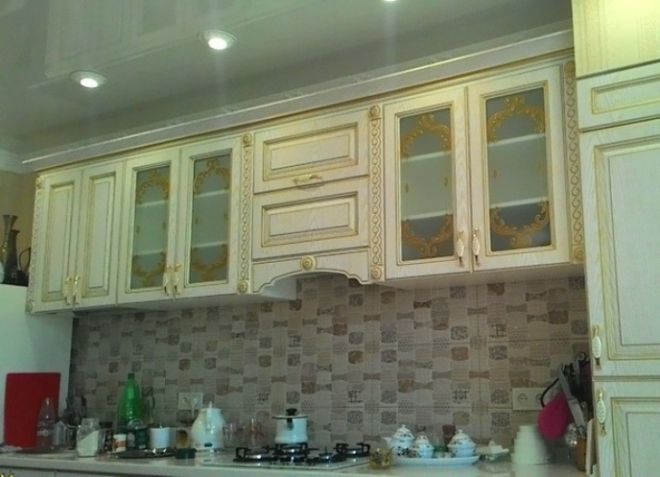
Facades of MDF play a big role in the design of premises. Matte, glossy, straight, curved, milled doors, decorated with glass or aluminum, will help create the style in the room. The material is waterproof, high strength, does not react with organic compounds, fungi and microorganisms. Due to the breadth of the assortment and the unique possibility of design solutions, the products have won love and popularity among consumers.